試作部品・開発部品の製作
当社は短い納期での少量(⼩ロット)⽣産に特化しており、試作部品や開発部品の製作をご希望のお客様にとって最適な⽣産体制を備えています。実際、これまで多くの試作部品、開発部品の製作ニーズにお応えして参りました。
当社では、ただお客様に言われたものを作るというだけではなく、これまでに蓄積したプラスチック成形のノウハウで、お客様の試作、製品開発に役立つご提案をさせて頂いております。
もちろん、試作、開発部品を2⾊成形やインサート成形で製作することもできますので、お気軽にご相談下さい。
- 試作部品や開発部品を少量(小ロット)で製作して欲しい
- 設計変更に迅速、柔軟に対応して欲しい
- 開発スケジュールにあわせて納品して欲しい
- 量産工程に入る前に、プラスチック成形のプロの視点を取り入れた試作部品、開発部品を製作したい
- 試作部品や開発部品を少量(小ロット)で製作して欲しい
- 試作部品や開発部品を2色成形やインサート成形で製作して欲しい
陣内⾦型⼯業の試作部品、開発部品の考え方
プロの視点
お客様からいただいた図面のものをそのまま作ればよいのではなく、お客様が直面するかもしれない問題点を、プラスチック成形のプロの視点から考え、ご提案しております。
プラスチック部品についての知識、ノウハウがない方でも当社の技術者がバックアップいたします。
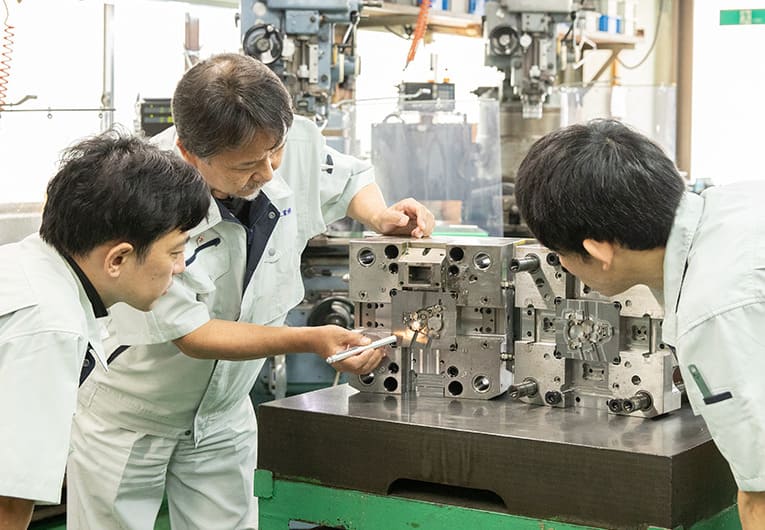
迅速な対応
開発・試作段階では設計変更が頻繁に起こることがあります。当社はそのような場合でも社内で金型を修正する機能を持っておりますので、迅速に対応することができます。
開発・試作に十分な予算や時間がとれない時代だからこそ、当社の対応力がきっとお客様のお役に立てるのではないかと思います。
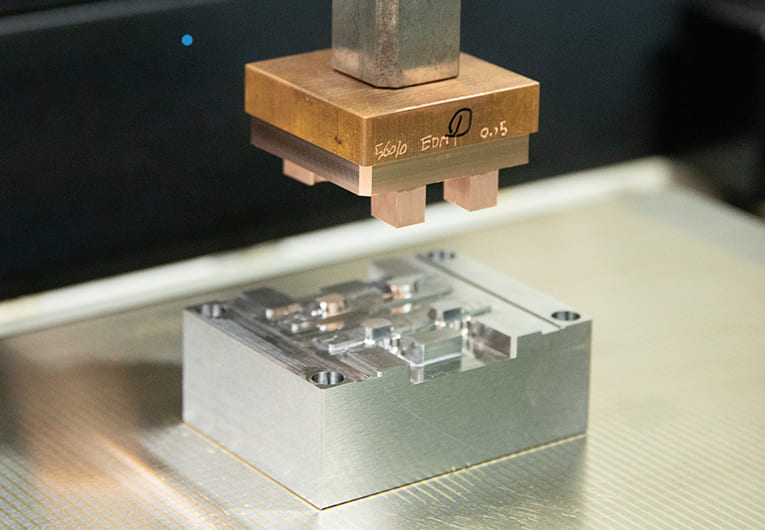
事例紹介
形状変更のご提案の事例
自動車部品メーカーA社の事例です。
当社に送られてきた図面データを見ると、用途に見合った強度が出ないのではないかという懸念を持ちました。お客様に確認したところ、その部品に関しては強度のことはあまり考えずに設計されたとのことでした。
そこで、当社から強度を補強するためリブを追加してはどうかという提案をいたしました。同時に、肉厚が必要以上に厚い部分を洗い出し、その部分の肉厚を薄くすることで、全体のコストが上がらないように工夫した形状に設計変更いたしました。
その結果、製品の強度を確保しつつ、コストを抑えることに成功し、お客様の試作・開発にかかる時間を短縮することができました。
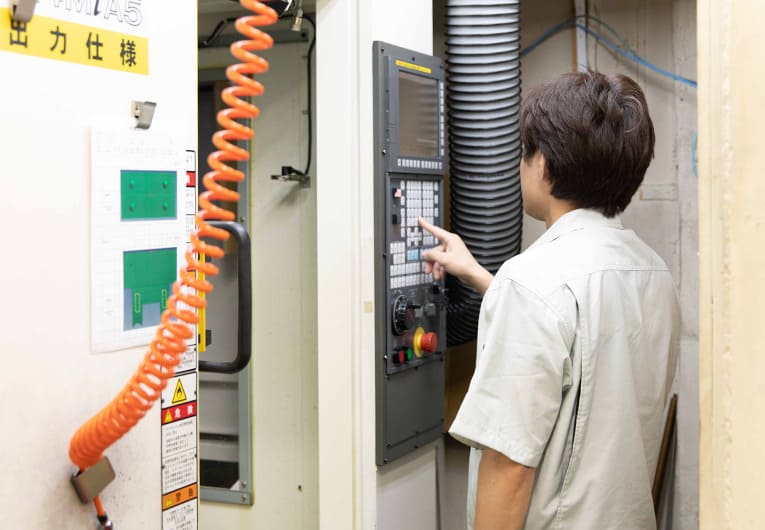
ゲート位置、ゲート方式変更の事例
産業機械メーカーB社の事例です。
いただいた図面での作成には何の問題も無かったのですが、ゲート位置(プラスチック材料の流入位置)が悪く、製品の品質に悪影響を及ぼす可能性があることが分かりました。
ゲート位置の変更を検討しましたが、当初考えていたピンゲート方式では、他の場所にゲート位置を設定しても無理があることが分かりました。
ゲートの方式としては、ピンゲート、サイドゲート、サブマリンゲート、ノーズゲート等の方式がありますが、当社では流動解析を行い、どの方式でどこにゲート位置を設定するのが、最も製品の品質を一定に保つことができるのかをシミュレーションしています。
今回のケースでも、シミュレーションの結果をお伝えし、最適なゲート方式・位置をご提案いたしました。
担当者からは「このまま量産工程に移っていたら大変なことになっていた。試作段階で気がついて良かった」とのお言葉をいただきました。
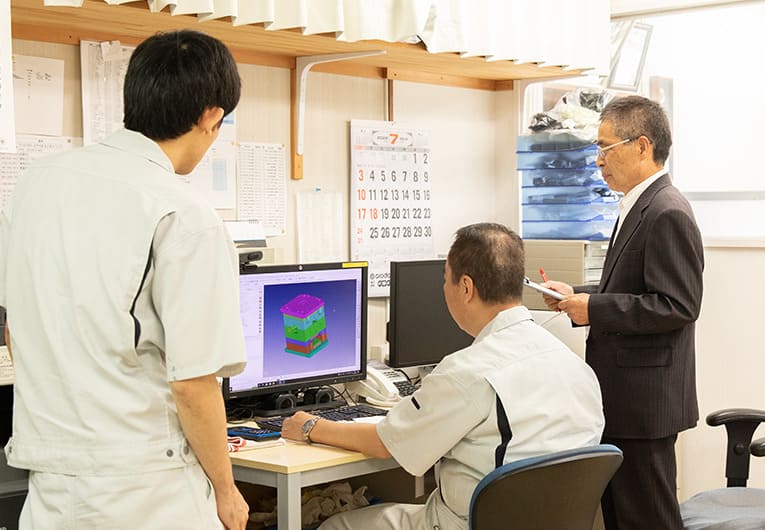
2色成形のご提案
医療機器メーカーC社の事例です。
複数の部品の試作を依頼され、仕様決定の打ち合わせを行いました。その際に、2つの部品が1つの機能を果たすものであることが分かりました。
2つの部品はそれぞれ使用する素材が異なるため、別々の部品にしたとのことでした。
そこで、2色成形(ダブルモールド)についてお話しさせていただき、2つの部品を1つの部品として成形することが可能であること、それにより、部品そのもののコストダウンはもちろんのこと、組立工程の工数が減ること、製品段階での不良発生率が低減することもご説明しました。
その結果、機械そのものの設計を見直し、2色成形で作成した部品を採用することになりました。
C社には2色成形部品のメリットを感じていただいたようで、その後も2色成形部品のご相談を受けております。
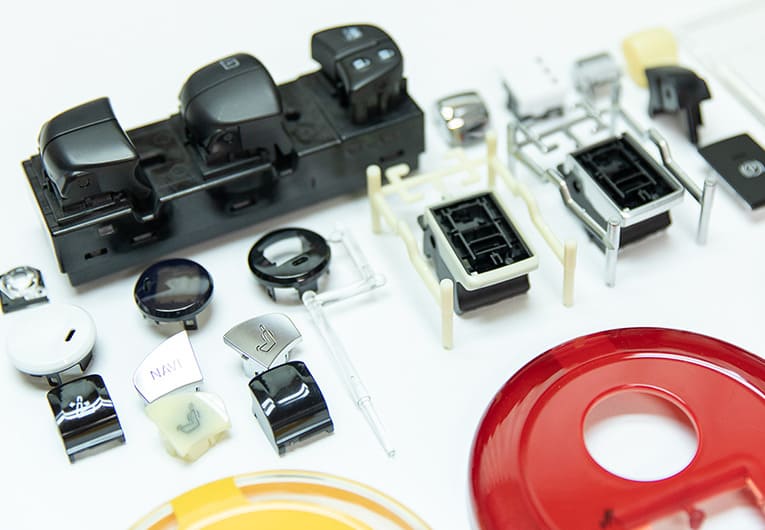
試作部品・開発部品発注の流れ
ご相談・お問い合わせ
まずはお気軽にお問い合わせください。
その際、CADで作成した図面データをご用意願います(手書きでも可)。
図面データをご用意いただけない場合、現物をお送りいただく形での対応になります。
納期/諸条件等も併せてお知らせ願います。
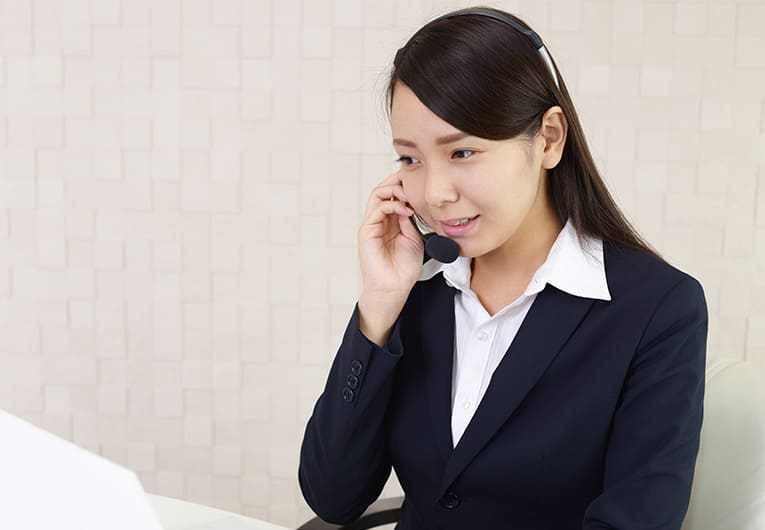
お見積・ご契約
頂いた図面からお見積書を作成いたします。
納期や納品場所等の条件もこのタイミングでご提示いたします。
お見積もり金額、諸条件にご納得いただいた上でのご契約となります。
ここから製品の製作がスタートします。
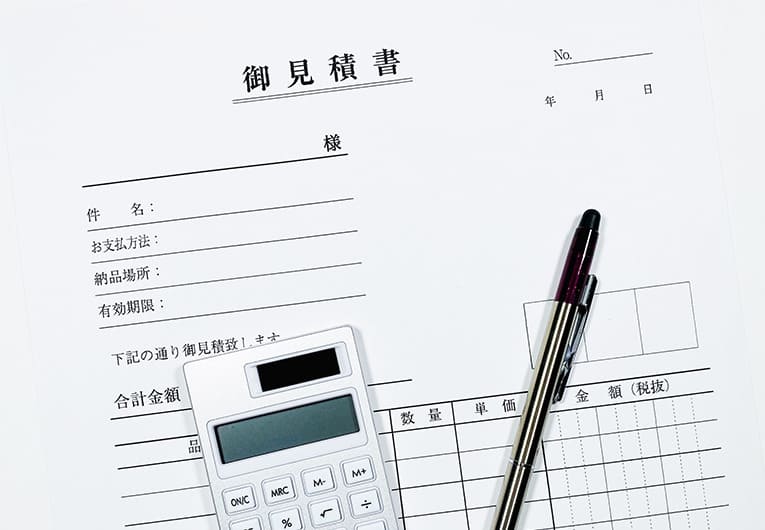
詳細な仕様の打ち合わせ
金型の製作に入る前に、お客様と仕様の細かな条件についての打ち合わせを行います。
技術的に不明な部分をここでクリアにいたします。
強度やコストなどに問題点があればプロの視点から丁寧にアドバイス・ご提案をさせていただきます。
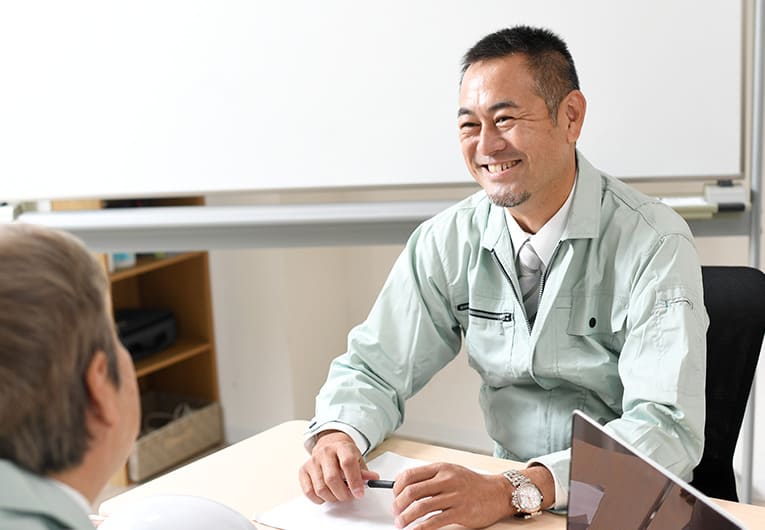
金型設計
打ち合わせの内容を元に金型の設計を行います。
陣内金型では自社で設計を行っておりますので、設計の変更などにもスピーディーに対応することが可能です。
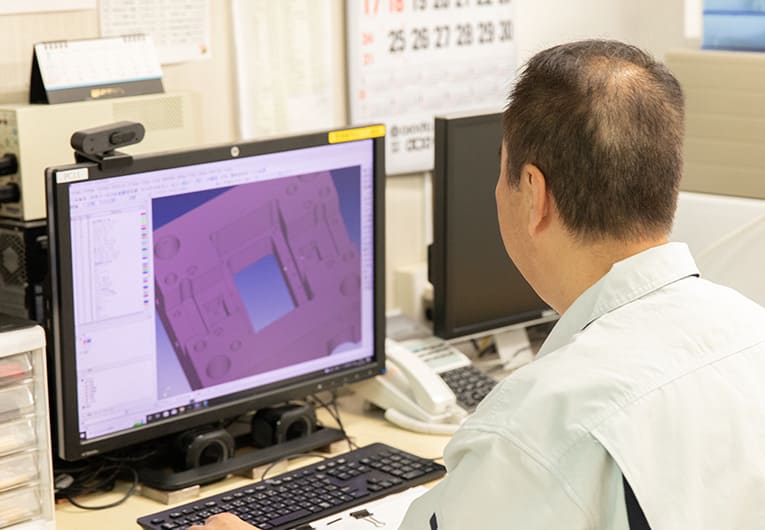
金型の作成・仕上・組立
一部を除き、基本的に社内で金型加工を行います。
金型の少しの精度の悪化も製品の品質に影響を与えます。微調整を行い、高精度な金型を仕上げていきます。
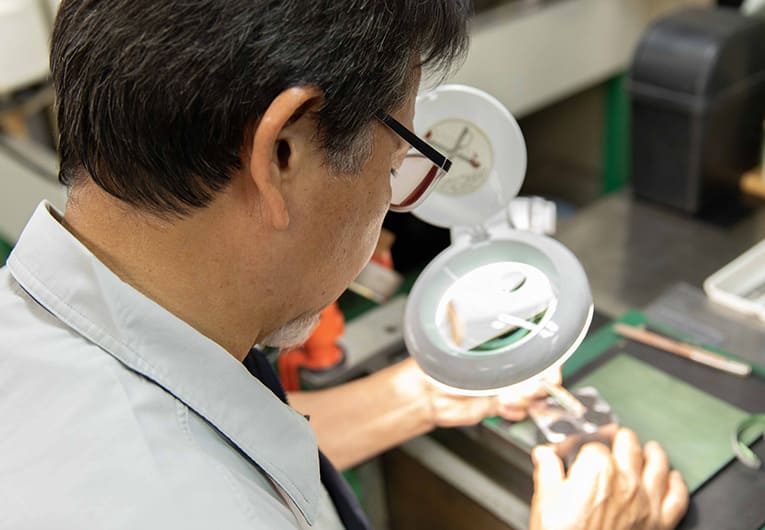
射出成形製品の作成
射出成形機に金型を取り付け、成形いたします。
当社は小ロット生産に最適化した生産体制を整えており、お客様のご要望に柔軟に対応いたします。
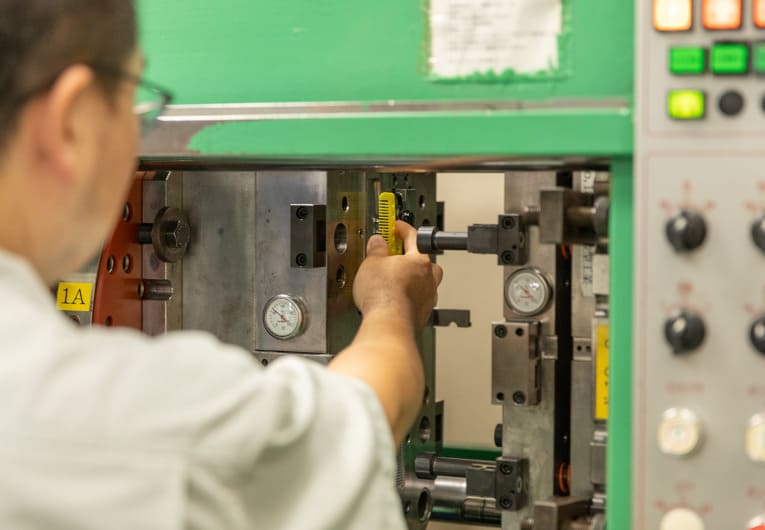
製品検査
画像測定器・測定顕微鏡等にて、検査を行います。
寸法測定結果をまとめ提出いたします。修正が必要な場合でも社内での迅速な対応が可能です。
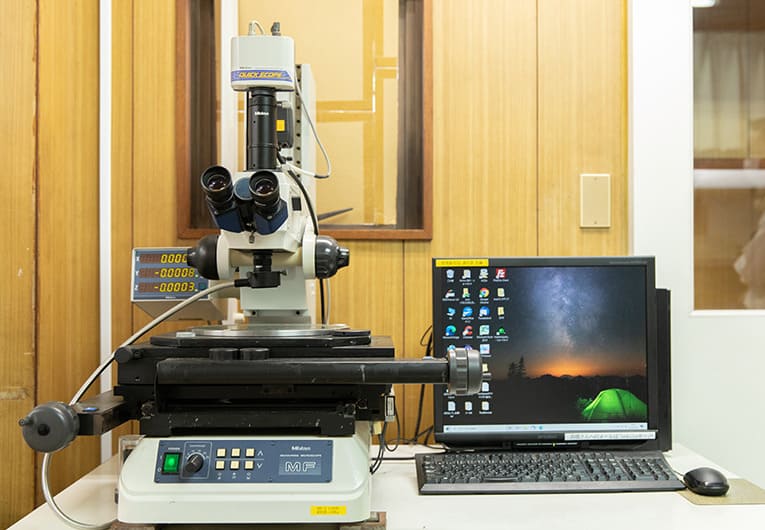
納品
お客様のご要望にもよりますが、
当社では金型完成後にトライ(形状確認等)を行い、外観/寸法/嵌合等の問題がなくなるまで修正を行います。
→お客様に確認後、良品を納品いたします。
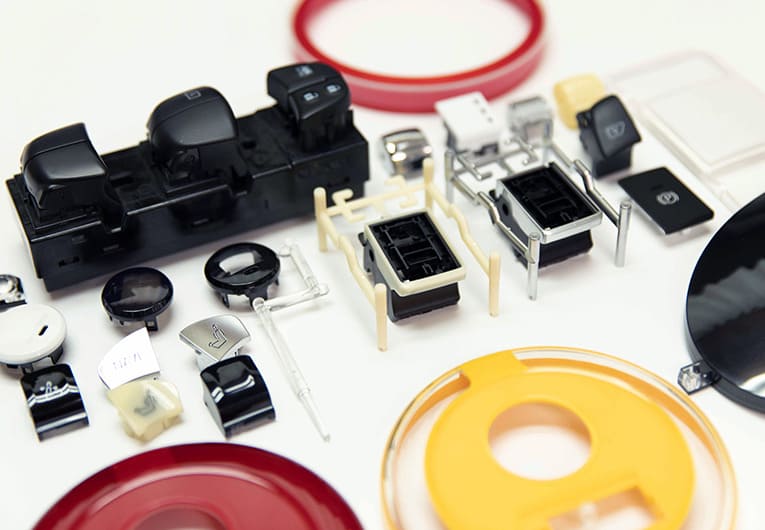